Flying cars might still be on the horizon, but much of what The Jetsons dreamed up in the 1960s—and again in the 1980s—has already become part of everyday life. Video calls, flat-screen TVs, smart devices, and robotic assistants have moved from science fiction to reality, reshaping the way we live and work. Now, Mississippi Agricultural and Forestry Experiment Station researchers, working with the Mississippi State Agricultural Autonomy Institute, are pushing that transformation even further—leading innovation in precision and autonomy in agriculture. From boosting productivity and efficiency to driving profitability for producers across Mississippi and beyond, MAFES is building the future of farming. Today's breakthroughs are laying the foundation for tomorrow's fully autonomous systems, ensuring agriculture continues to thrive for generations to come.
Bots versus Bags
That plastic bag or piece of a cotton module wrap you see in a cotton field might not look like much, but to farmers, it represents a costly challenge—one that contributes $600—$750 million in annual losses across the industry.
Dr. Brian Pieralisi, plant and soil sciences assistant professor and MAFES scientist, said the issue directly affects growers' bottom lines.
"If plastic debris is detected in a cotton sample, it's an immediate $0.40 per pound deduction—that's a direct loss of about $200 per bale for the grower," he said.
To help cotton producers cut costly losses, Pieralisi is working with MAFES scientists Drs. Hussein Gharakhani and Wes Lowe to develop a modular unmanned ground vehicle (UGV) that removes plastic contamination before harvest. Led by Gharakhani, assistant professor of agricultural and biological engineering, the project integrates AI and robotics into field-ready tools, with a modular design that can later be adapted for tasks like weeding and replanting.
"We are building a collaborative system between a UAV [unmanned aerial vehicle] and a UGV. The UAV scouts the field, collects images, finds hotspots, and then identifies a path for the UGV to follow and remove the contaminants," Gharakhani said.
Plastic contaminants in cotton fields typically come from two sources—module wrap and roadside litter, such as grocery bags and snack wrappers. To train the system, researchers found real-world contaminants in test fields and captured images from multiple angles and lighting conditions.
"We trained our model on real-world contaminants we found in the field, already weathered and dirty instead of clean bags from a store," Gharakhani said. "Our object detection model can detect 82.4% of plastic bags. We're working to improve that."
The team found that 49% of plastic contaminants found in the sample fields were entangled in the plants, which Gharakhani noted is a big issue for producers.
"If a cotton picker encounters a plastic bag, it either picks it up-contaminating the bale—or it lifts the header, which means you may lose several rows of cotton for a certain distance that won't get harvested. Either way, it's a loss." Gharakhani said. "We designed the UGV to fit between two cotton rows and built it with narrow sides—just 30 centimeters wide—so it doesn't disturb the crop while navigating."
The team is also building a robotic arm and end-effector that will be a part of the UGV, which will accurately localize plastic bags and retrieve them. The system will be tested both in the lab and in the field.
Lowe, an assistant professor in agricultural and biological engineering, said the technology has long-term potential.
"We could eventually deploy multiple UAVs and UGVs working together—like a swarm—to manage entire fields. This could actually become a production-level solution," Lowe said. "At the end of the day, we're trying to give farmers more tools so they can minimize inputs, maximize returns, and stay in business year after year."
Berry Smart
Dr. Xin Zhang, assistant professor of agricultural and biological engineering and MAFES scientist, is leading advancements in robotics and artificial intelligence (AI) to develop automated solutions for harvesting blackberries.
In collaboration with Georgia Tech and the University of Arkansas, Zhang helped develop a smart robot that uses a vision system to detect ripe berries and pick them gently to avoid damage. Built on the YOLOv8 (You Only Look Once) object detection model, the technology identifies ripe blackberries with 94% accuracy.
To advance this work, Zhang recently welcomed doctoral student Jonathon Harjono to further refine the computer vision system for harvesting blackberries. Zhang explained that developing these systems comes with challenges.
"A key technical challenge is the vision system. In automated cars, models are trained with millions of images, but in agriculture, we often have access to hundreds or thousands of images. We also rely on locally collected images, and when models trained on them are used in other regions, differences in crop architecture and planting can cause them to fail. Building diverse, robust datasets is still a major hurdle," she said.
To address this, the team is integrating advanced AI technologies like Generative Adversarial Networks, or GANs, to create synthetic images from real-world examples.
"The size of the dataset is a bottleneck, so we want to use this generative AI tool to generate realistic enough images, and we'll likely expand a little more using other AI models," she said.
Zhang's contributions to the field extend beyond the lab. She recently authored a chapter in Advances in Agri-Food Robotics, published by Burleigh Dodds Science Publishing. Her chapter, "Advances in the Use of Robotics in Orchard Operations," explores leading-edge technologies for robotic harvesting in orchard environments.
Her research focuses on enhancing deep learning vision systems to recognize and analyze orchard canopies, even under challenging conditions like low light or obstructive foliage. Zhang emphasizes the critical role of tree architecture in advancing automation.
"Tree structure matters," Zhang said. "In Washington, growers have adopted 'fruiting wall' systems that flatten the canopy into a planar form. This design dramatically improves mechanical and robotic access."
In her chapter, Zhang highlights progress in navigation and vision-based systems.
"Vision-based navigation using RGB and RGB depth cameras has come a long way. While not as accurate as LIDAR, we can get a RGB depth camera for $500, while LIDAR equipment costs around $5,000," she said.
She also discussed situational awareness and operational management in agricultural robotics.
"In agriculture, different tasks require different solutions, especially for machine vision systems. The vision system identifies where objects are and where the end effector needs to go," Zhang explained. "We discuss using machine learning, deep learning, and AI for object and obstacle detection, canopy interpretation, fruit harvesting, automatic pruning, and flower detection for blossom thinning. Computer vision at night also enables bots to pick fruit 24/7."
At the core of Zhang's work is a passion for interdisciplinary collaboration.
"Growers and plant scientists define the needs, engineers build the tools, and data scientists interpret the results," she said.
"That's how innovation happens."
The team plans to expand to raspberries, loganberries, and other berry varieties.
Smart Spud System
Sweetpotato production is one of the most labor-intensive operations in agriculture—and the rising cost of labor reflects that. Compared to traditional row crops, labor expenses for sweetpotatoes are 60 times higher. Between 2020 and 2023, the average Mississippi sweetpotato producer spent $350,000 more on labor, adding up to a $12 million increase across the state.
Dr. Lorin Harvey, assistant professor in plant and soil sciences at the MAFES Pontotoc Ridge-Flatwoods Branch Experiment Station explained the increase.
"The costs of labor in sweetpotatoes have increased so much for two main reasons. First, as growers lose chemical control options and consumer preferences tighten, more labor is needed to ensure a quality product gets delivered to consumers' tables. Second, Department of Labor increases in H2A labor rates between 2019 and 2024, specifically the Adverse Effect Wage Rate (AEWR) paid to H2A workers has risen 31%," Harvey said.
To help offset these costs, MAFES researchers, including Harvey, are developing a robotic harvesting solution for sweetpotatoes that supplements current methods while improving efficiency and reducing reliance on manual labor.
Dr. Hussein Gharakhani, assistant professor in agricultural and biological engineering, leads the effort alongside Harvey and Dr. Wes Lowe, also an ag and bio engineering assistant professor.
"Sweetpotato growers have the highest expenditure of labor costs, around $1,000 per acre just in labor. It's particularly bad around harvest. While we don't intend to replace traditional harvest methods, we do hope to supplement them to offset some of these high costs," Harvey said.
Current harvest techniques use a combination of mechanical and manual labor. In one common method, a flip plow digs in the soil, takes the sweetpotatoes out of the soil, and drops them on top of the soil, leaving them for bucket crews to collect and sort. Another system, the chain digger harvester, lifts the potatoes with a blade and carries them up a vibrating chain conveyor. The roots are sorted manually—an approach that presents safety risks and limits productivity.
To improve the process, the MAFES team is designing a mobile rover equipped with a perception system; a 4 degrees of freedom robotic arm; and an end-effector to locate, pick, and sort sweetpotatoes. The system will also include a conveyor that rotates and inspects each root after harvest.
The team faces a range of technical challenges. Sweetpotatoes vary widely in shape, size, and weight, and are often tangled in vines or coated in soil—making automated detection and handling difficult. While the original plan involved mounting a robot on a chain digger, the team decided to move toward an independent rover platform, making it easier to test and validate the system inside the laboratory and in the field.
"As humans, each of our arms and hands—left and right—has approximately 27 degrees of freedom, independent movement capabilities," Gharakhani explained. "One of the biggest challenges is designing an arm and end effector—something that can gently pick up sweetpotatoes of all shapes and sizes, sometimes connected by vines, sometimes covered in soil. That's not easy."
Now, the team is developing a ground-based rover with simplified motion and improved flexibility, designed for real-world deployment.
"We want to replace the bucket crew with a rover. The rover will go into the field, pick up the sweetpotatoes, and put them in a container—no bucket, no running, just autonomy," Gharakhani said.
"Sweetpotatoes in general do not have access to the automation and the technology that a lot of the major row crops or the higher value specialty crops do," Harvey added. "I love working to bridge the gap between science and an actual problem and helping find a solution to that problem."
Gharakhani sees robotics and autonomy as essential to helping feed the world.
"We don't have any other choice. To feed 10 billion people by 2050, we need solutions that work with nature—not against it. Leveraging robotics and autonomy is the only way forward," Gharakhani said.
The world George Jetson imagined is closer than ever, as MAFES researchers lay the groundwork for farms that are smarter, more sustainable, and better equipped to feed and clothe a growing world.
Bot Versus Bags is funded by Cotton Incorporated and the U.S. Department of Agriculture's Agricultural Research Service. Graduate students supporting the research include Md. Sazedur Rahman, who works on training UAV and UGV-based object detection models, as well as robotic arm and end-effector development, and Asifur Rahman, who works on UGV modification, as well as a path planning algorithm and navigation system development. Berry Smart is funded by the USDA National Institute of Food and Agriculture National Robotics Initiative 3.0 (NRI-3.0) program in partnership with the National Science Foundation. Smart Spud System is funded by the U.S. Department of Agriculture's Specialty Crop Block Grant program. Master's student Ammar Hadwan is also contributing to the project, which is funded by the Mississippi Department of Agriculture and Commerce and the Mississippi Agricultural and Forestry Experiment Station.
Sweetpotato growers have the highest expenditure of labor costs, around $1,000 per acre just in labor. It's particularly bad around harvest. While we don't intend to replace traditional harvest methods, we do hope to supplement them to offset some of these high costs.
Dr. Lorin Harvey
Behind the Science
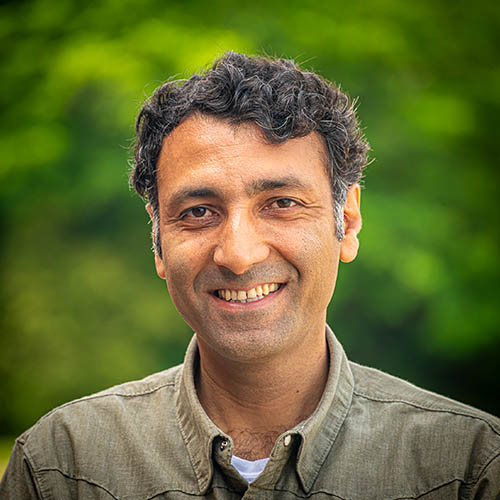
Hussein Gharakhani
Assistant Professor
Education: B.S., Agricultural Machinery Engineering, University of Tabriz; M.S., Mechanical Engineering of Agricultural Machinery, University of Tehran; Ph.D., Biosystems Engineering, Mississippi State University
Years At MSU: 5
Focus: Agricultural robotics and autonomy
Passion At Work: I love agriculture, and I love machines — agricultural engineering brings both together. Agricultural robotics and autonomy empower us to produce more efficiently, reduce labor demands, and protect our natural resources.
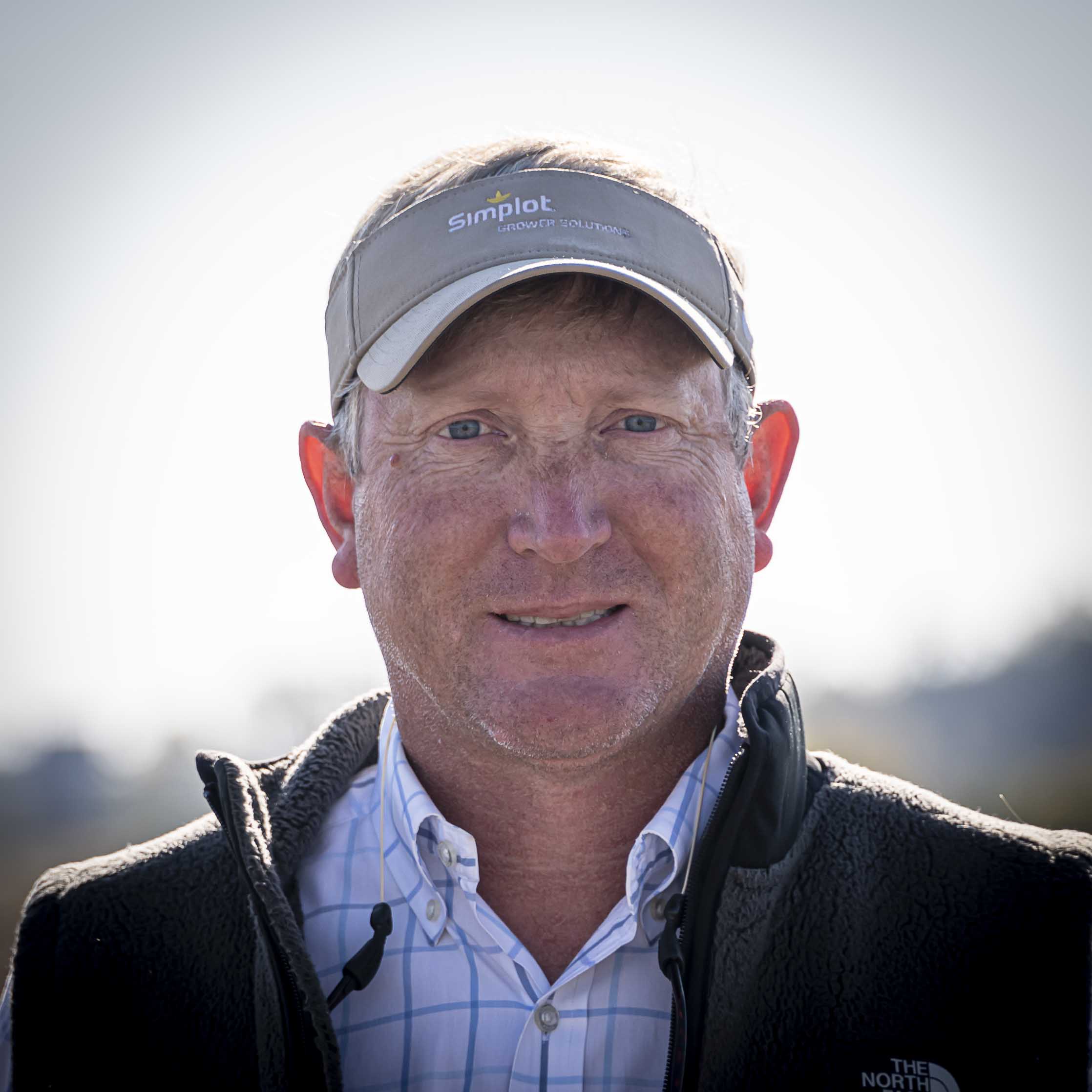
Wes Lowe
Assistant Professor
Education: B.S., Agricultural Engineering Technology and Business; M.S., Agriculture; Ph.D., Agricultural Sciences, Mississippi State University
Years At MSU: 20
Focus: Applied research in precision agriculture and machinery systems
Passion At Work: My research focuses on leveraging technology to develop solutions that improve cropping systems and positively impact economic returns for our agricultural producers.
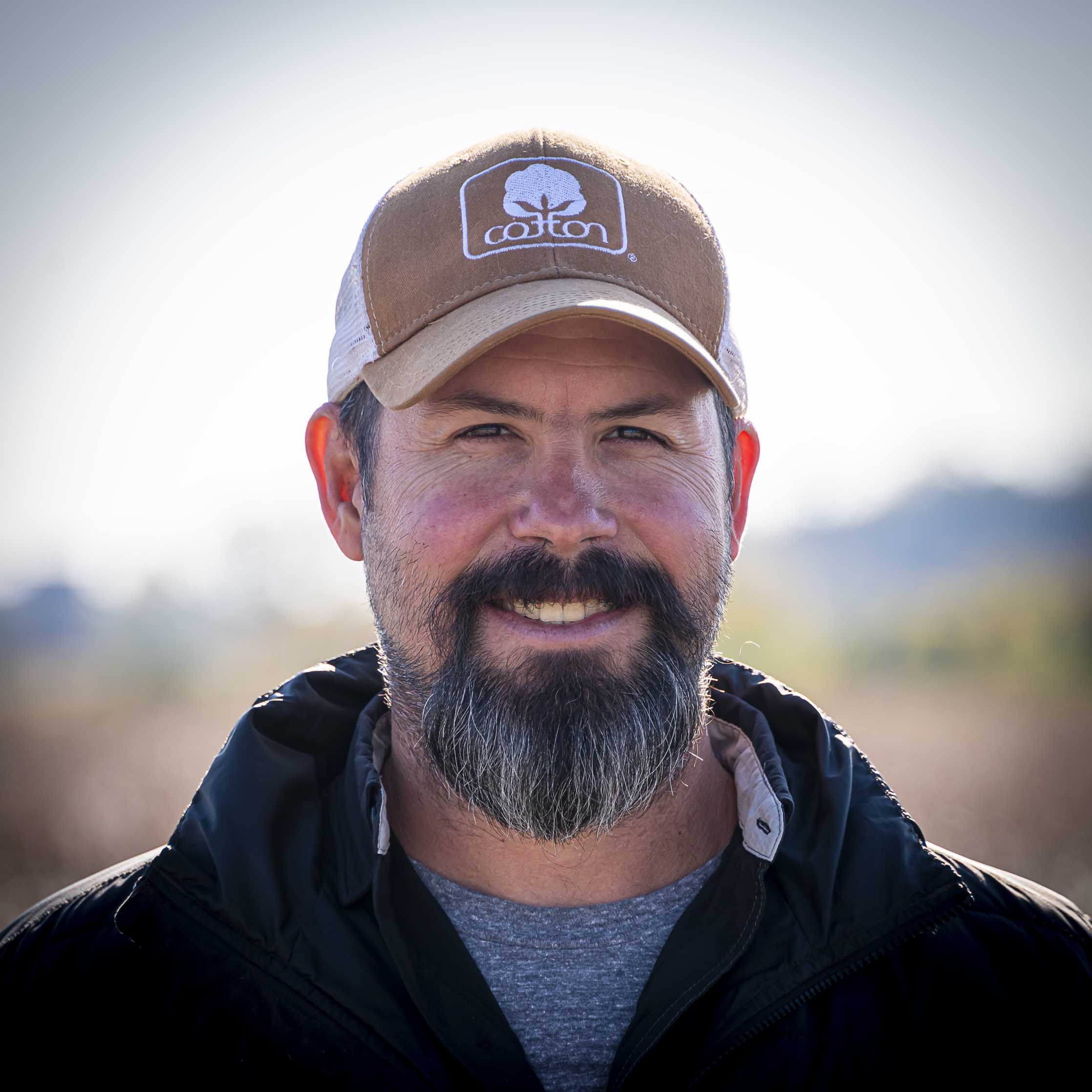
Brian Pieralisi
Assistant Professor and Extension Cotton Specialist
Education: B.S., Ag Pest Management, Mississippi State University; MBA, Delta State University; Ph.D., Agronomy, Mississippi State University
Years At MSU: 5
Focus: Cotton variety testing and graduate student research, which encompasses all aspects of agronomy
Passion At Work: Teaching graduate students. It's the best of both worlds. You can conduct research in the field you love and have eager minds wanting to learn.
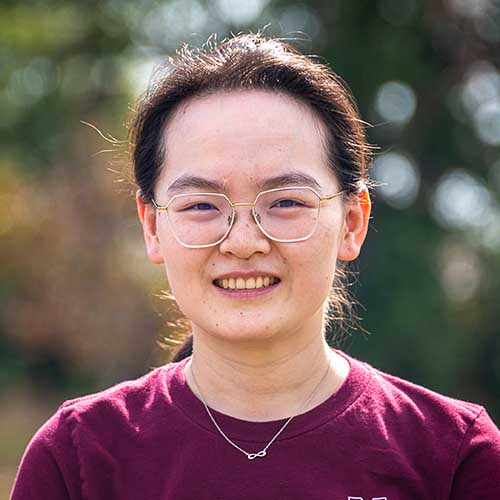
Xin Zhang
Assistant Professor
Education: B.S., Agronomy in Facility Agriculture Science and Engineering, Gansu Agriculture University; M.S. of Agriculture, Horticulture Engineering, Northwest A&F University; Ph.D. of Biological and Agricultural Engineering, Agricultural Automation Engineering, Washington State University
Years At MSU: 3.5
Focus: Digital agriculture; agricultural robotics; computer vision; AI in agriculture
Passion At Work: I am passionate about advancing digital agriculture and agricultural robotics to transform farming practices, enhance productivity, and ensure sustainable agricultural systems through engineering and technological innovations.
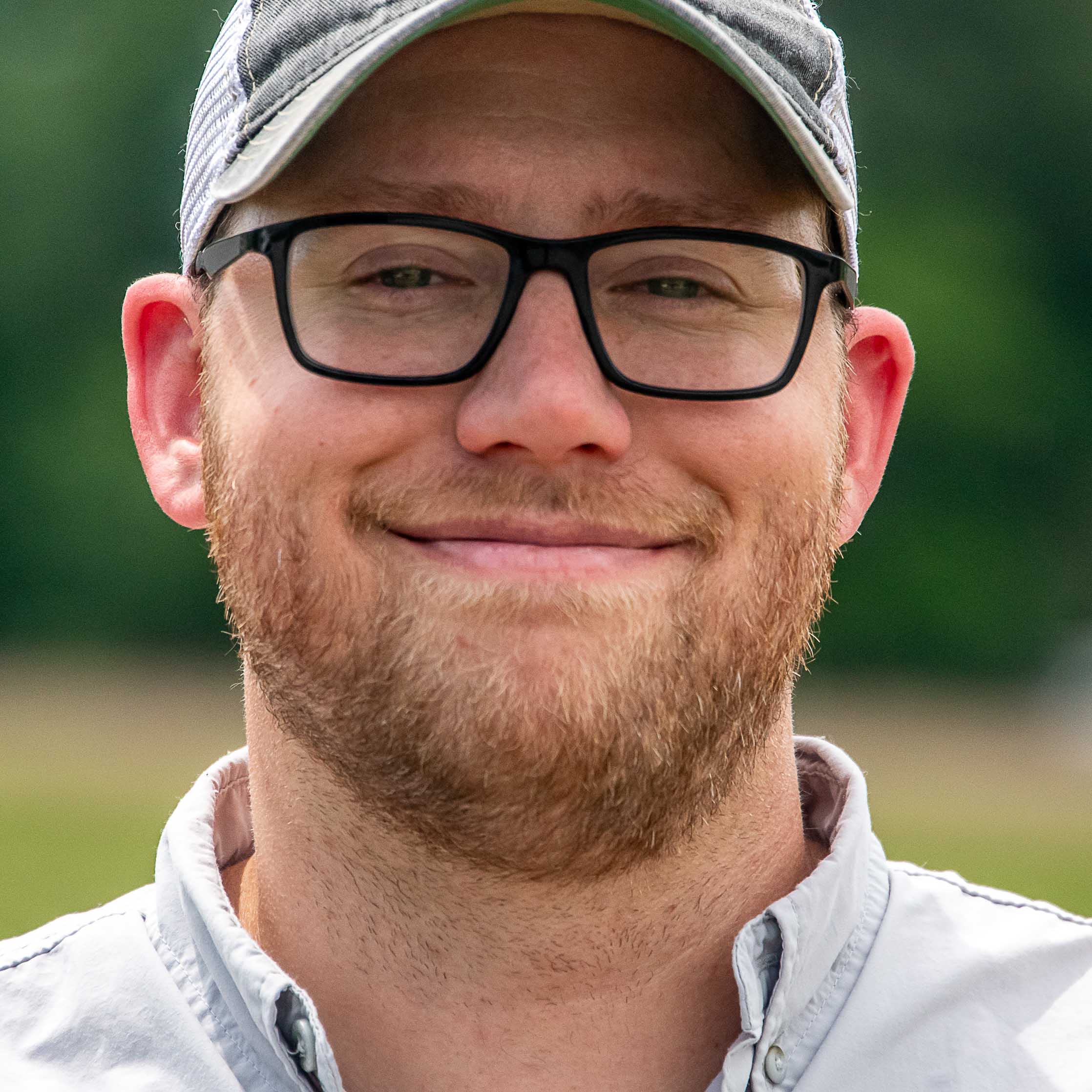
Lorin Harvey
Assistant Professor and Extension Sweetpotato Specialist
Education: B.S., Agronomy, Iowa State University; M.S., Ph.D., Plant Breeding and Genetics, Texas A&M University
Years At MSU: 4.5
Focus: All things sweetpotato
Passion At Work: Addressing real-life on-farm challenges through applied research and extension programs.