The information presented on this page may be dated. It may refer to situations which have changed or people who are no longer affiliated with the university. It is archived as part of Mississippi State University's history.
The Mississippi Agricultural and Forestry Experiment Station's (MAFES) 200 cows are milked twice a day, 365 days a year to produce 369,000 gallons of milk annually. Managing herds this size and larger has traditionally been a labor-intensive undertaking for both the dairy and beef cattle industries. But Mississippi State University (MSU) scientists have a solution afoot that could make the work more efficient and less physically demanding while resulting in greater wellbeing for the cattle.
A cross-departmental effort is underway to apply the advancing technology of autonomous agriculture—used widely in farming—to the "dirty work" of driving cattle. For the last year, MAFES scientists, in collaboration with scientists in the MSU Center for Advanced Vehicular Systems (CAVS) and the Raspet Flight Research Lab, have been investigating the potential use of unmanned ground vehicles (UGVs) as a safer and more efficient means of livestock movement and management.
Dr. Marcus McGee, principal investigator and assistant clinical professor in the Department of Animal and Dairy Sciences (ADS), and Dr. Christopher Hudson, co-principal investigator and research engineer at CAVS, have conducted a series of trials at the MAFES Joe Bearden Dairy Research Center with a Clearpath Robotics Warthog UGV equipped with cameras and sensors.
During these initial trials, the team manually operated the UGV to move the herd of dairy cows, which are conditioned to daily human interaction. The scientists wanted to first observe how the cows would respond to the robot before pursuing autonomous technology.
Just because you build it doesn't mean that they will—in this case—go. But the animals' behavior around the Warthog during the trials shows signs of their acceptance and willingness to be moved by a machine.
"To our surprise, the animals were calm around the Warthog and behaved the same way they would around a person on horseback or driving a four-wheeler," said McGee.
"Young calves don't have the strong herd instinct that mature animals do, but we saw that in the presence of the robot, these calves moved along like a herd—not scurrying in fear but loping along together."
This fall, faculty from ADS, CAVS and the Agricultural Autonomy Institute applied for a USDA National Institute of Food and Agriculture (NIFA) Interdisciplinary Engagement in Animal Systems grant. The collaborative effort, if funded, will advance the initial study—determining how conventional herding principles might apply to robots and developing guidelines for operating autonomous herding vehicles. Since there are no guidelines for this kind of technology, the study would place MSU at the forefront of this up-and-coming area of research.
"If you're designing a self-driving car, it follows the rules of the road, which have been established over many decades," said Hudson. "We don't have rules for how one vehicle, let alone a team, should work to detect, see, and move cows."
Developing these guidelines alone is a monumental undertaking, but it's just one step in the larger effort to manage cattle autonomously. Rather than performing a single task, these robots have the potential to assist producers and technicians with husbandry practices containing multiple levels of complexity. They will not only move the herd from point A to point B but will also keep tabs on individual cows, monitoring behavior and health.
To this end, ADS and CAVS faculty are mentoring two Undergraduate Research Scholars Program students, investigating the use of machine learning algorithms to identify individual dairy cows in a herd and flag mounting behaviors.
"Identifying individual cows is a critical piece of the puzzle," said McGee. "We're not only looking to robots to herd cattle but also to record behaviors and associate health related data to specific cows."
Beyond the primary task of herding, a UGV could monitor the health of individual animals more frequently and with more precision than humans can, thus expediting medical treatment.
"An autonomous system equipped with cameras and thermal sensors could potentially detect illness or injury, and that data could help us identify who needs to be separated from the herd and when we should notify the farmer or veterinarian," said McGee.
The scientists are currently analyzing their video data for a variety of aspects related to both animal behavior and robot-animal interaction, and they hope that data will yield solid results within the next few months. They also plan to replicate the trials using differing age groups in hopes to gain further insight about the animals at each developmental stage.
Although the research is still in its infancy, UGVs will clearly become a game changer for the livestock industry, much like precision agriculture technology is changing how crops are grown and monitored today. As with agriculture, livestock management relies on repetitive tasks performed at the same time every day, and these tasks lend themselves well to automation.
"Herding cattle can be dangerous, and it's getting more difficult each year to keep people employed doing these types of manual tasks," said Hudson.
"We see this as an area where robots can make a positive impact as a workforce multiplier by doing the repetitive manual jobs. As the technology is expanded, the potential to create higher-paying technical jobs will evolve."
"In the next decade or so, we may see livestock producers working alongside engineers and computer scientists," added McGee. "Jobs in the industry's future will likely be very different from the ones we have today with increased adoption of precision livestock management."
While the end goal of autonomous herding lies on the horizon, these scientists see their work as building the foundation—the rules of the road—that will allow for the successful deployment of existing robotics technology in a livestock setting.
"At Mississippi State, we work together across disciplines to solve pressing issues, including the ability to augment skilled labor in the workforce," said Hudson.
"Because of our excellence in agriculture, engineering, and unmanned systems, MSU is uniquely qualified to be a leader in this emerging field of research."
This research is funded by the Mississippi Agricultural and Forestry Experiment Station.
An autonomous system equipped with cameras and thermal sensors could potentially detect illness or injury, and that data could help us identify who needs to be separated from the herd and when we should notify the farmer or veterinarian.
Dr. Marcus McGee
Behind the Science
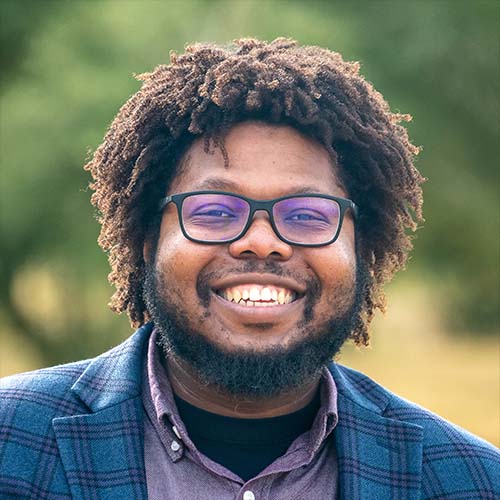
Marcus McGee
Assistant Clinical Professor
Education: B.S., M.S., Animal Science; Mississippi State University; Ph.D., Animal Physiology, University of Idaho
Years At MSU: 2
Focus: Animal physiology, precision livestock management, behavior, and welfare
Passion At Work: To adopt emerging technologies in the livestock sector to enhance the wellbeing and sustainability of production efforts.
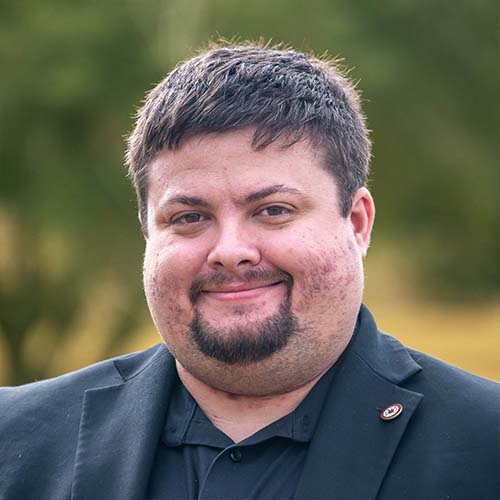
Christopher Hudson
Research Engineer III
Education: B.S., Computer Science, University of North Carolina at Pembroke; Ph.D., Computer Science, Mississippi State University
Years At MSU: 6
Focus: Off-road unmanned ground vehicles
Passion At Work: Enabling autonomy in challenging off-road environments to serve as workforce multipliers to improve efficiency and safety.